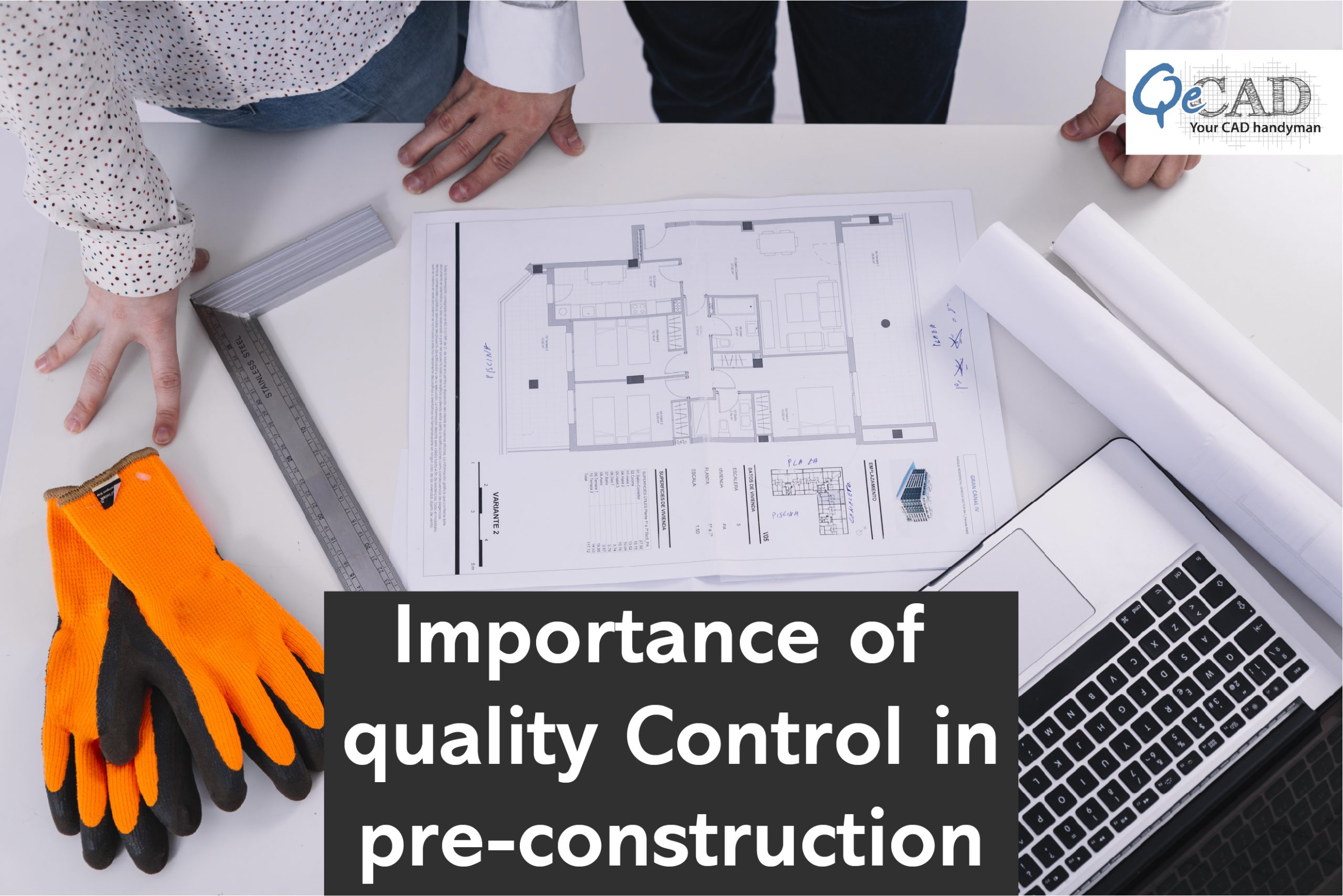
Introduction
In the construction sector, quality monitoring is crucial. The machines, supplies, and other items used on the construction site must also meet the highest quality, safety, and proper functional requirements. But, maintaining them correctly during the time the project is underway is highly significant.
Thankfully, there are an extensive number of ways to guarantee building quality assurance. You’ll discover the value of product testing in the construction sector, or Digital Construction Company, and its methodologies in this brief article.
What Exactly Is Pre- Construction Quality Assurance?
Pre-construction quality administration is essential since the sector is controlled. Also, it contributes to the building’s safety, functionality, & completion on time frame and budget.
It’s critical to comprehend the value of quality assurance in building as well as what it entails. But not just construction firms are capable of performing high-quality work. It encompasses their business associates as well as other participants in the building distribution chain. It entails examining the calibre of the work produced by building contractors and subcontractors—even the importation of tools, supplies, Rendering Services, and other items utilized on site.
Quality management and successful outcomes are the two basic categories into which quality control in architecture can be divided. While quality monitoring generally alludes to achieving existing regulatory criteria, quality control concentrates on the high standard of the good or service.
The relevance of quality standards in the pre-construction stage
The site must be adequately maintained, and all required permits must be secured before construction can start. This is why quality assurance is so important. It’s crucial to confirm that the tools and supplies utilised in the construction process are of the right quality and comply with the necessary requirements. Some other important factors are mentioned below:
- To adhere to guidelines
Pre-Construction quality assurance guarantees that the work is built in compliance with architectural plans & detailed design, so the finished project meets the requirements of the customers. So many important decisions about the integrity of a finished structure are made during the planning and development phases rather than throughout building development, as is the case with cost control. At these early stages, decisions are made on device layouts and technical specifications. Assuring adherence to these initial conceptual and strategic selections constitutes a substantial portion of quality assurance throughout building development.
- To lower expenses
Construction-related flaws or breakdowns can lead to significant financial losses. Reconstruction could be necessary, and site functioning could be hampered by even small flaws. Constructability management may reduce wastage and reworking amounts, lower the price, and boost performance and productivity efficiency to assist in lowering building costs.
- To reduce the number of accidents on construction sites
Actions taken during the preliminary stages of planning and design have a significant impact on safety throughout the building’s construction. An advantage of building quality assurance is this. For instance, keeping zones of construction well separated from traffic throughout roadwork can significantly lower the risk of accidents.
- For recognition
The reputation of both the customer and the provider improves when perfection is delivered. Being recognised as a provider of excellence has no comparable benefit.
- For improved outcomes
Greater outcomes can be achieved by fully engaging all participants in achieving quality, from customers to employees. Views are respected, and fresh ideas are examined and implemented
- Enhanced Effectiveness
Construction quality management makes sure that the work is carried out in accordance with the specifications and drawings, which can boost the effectiveness of the building process. This may lead to the project finishing on budget and on schedule.
Conclusion
We are all aware of the significance of construction quality. Pre- Construction quality control practices not only reduce the likelihood of disruptions. But it also makes certain that the undertaking satisfies the requirements and desires of the client. Performing examinations of the tools and supplies utilized during the construction process is one typical quality assurance technique. A profitable building endeavor depends heavily on quality assurance, which must be followed from project initialization and planning through its execution and completion. Evaluation throughout building projects will reduce the need for high maintenance costs after the job is finished.