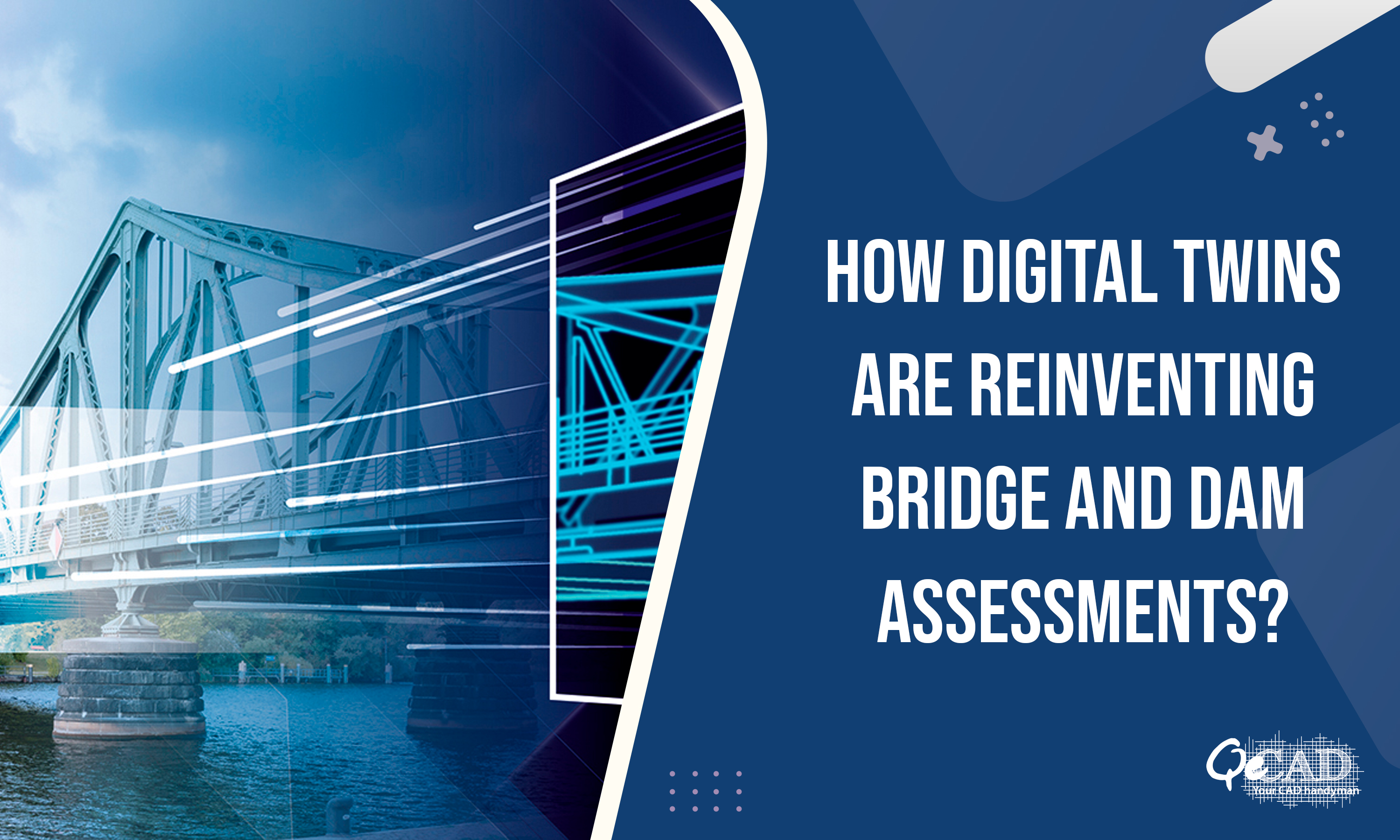
Introduction:
Considering the domain of civil engineering and infrastructure management, the advent of digital twin technology has revolutionized traditional inspection workflows for bridges and dams. A digital twin is a virtual representation of a physical object or system, and its integration into inspection processes has significantly enhanced efficiency, accuracy, and safety.
The below blog explores the transformative impact of digital twins on inspection workflows for bridges and dams, shedding light on the benefits and advancements this technology brings to the infrastructure management sector.
I. The Evolution of Inspection Workflows:
Historically, bridge and dam inspections have relied on manual methods, involving visual assessments, physical measurements, and on-site evaluations. Although these approaches have proven successful, they are lengthy, labour-intensive, and sometimes pose safety risks for inspectors. The integration of digital twin technology addresses these challenges by providing a comprehensive and dynamic virtual model of the structure.
II. What Are Digital Twins?
Digital twins are computer-generated replicas of tangible objects or systems, capable of simulating their behaviours in real-time. In the context of bridges and dams, a digital twin encompasses a detailed 3D model of the structure, coupled with sensor data, historical information, and real-time monitoring capabilities. This creates a holistic representation that allows engineers and inspectors to assess the health and performance of the infrastructure more efficiently.
III. Benefits of Digital Twins in Inspection Workflows:
- Enhanced Visualization: Digital twins provide a detailed and interactive 3D visualization for BIM for Infrastructure like bridges and dams, allowing inspectors to explore every BIM model component virtually. This level of detail enables a more thorough analysis of structural elements, identifying potential issues that may be overlooked in traditional inspections.
- Real-time Monitoring: Integrating sensors into the physical structure allows for real-time monitoring of different parameters including strain, temperature, and vibration. This continuous data stream enhances the ability to detect early signs of structural degradation or potential failures, enabling proactive maintenance and minimizing risks.
- Predictive Analytics: By utilizing historical data and employing machine learning algorithms, digital twins can anticipate potential future issues. This proactive approach to maintenance ensures that necessary repairs or upgrades are implemented before a problem escalates, reducing downtime and extending the lifespan of the infrastructure.
- Remote Inspection Capabilities: Digital twins enable remote inspections, minimizing the necessity for physical presence at the location. Inspectors can assess the structure from a safe distance, minimizing exposure to hazardous conditions and improving overall safety. This is particularly valuable in challenging environments or during adverse weather conditions.
- Data Integration and Collaboration: Digital twins serve as centralized repositories for all relevant data, including design specifications, maintenance records, and inspection reports. This integration streamlines collaboration among engineering teams, allowing for more informed decision-making and efficient communication.
IV.Case Studies: Successful Implementations of Digital Twins
- The Forth Road Bridge, Scotland: The Forth Road Bridge implemented a digital twin to monitor structural health and conduct inspections more effectively. Real-time data from sensors embedded in the bridge allowed engineers to detect and address issues promptly, minimizing disruptions to traffic and ensuring the safety of the structure.
- Hoover Dam, USA: The Hoover Dam utilized digital twin technology to monitor various parameters such as concrete health, water levels, and structural stability. This proactive approach has enhanced the dam’s resilience and contributed to the efficient management of water resources in the region.
V. Challenges and Future Prospects:
While digital twins offer numerous benefits, challenges such as data security, standardization, and initial implementation costs need to be addressed. Additionally, ongoing advancements in technology, including the integration of artificial intelligence and augmented reality, hold the potential to further enhance the capabilities of digital twins in bridge and dam inspections.
Conclusion:
Digital twin technology in integration with BIM Services is reshaping the domain of bridge and dam inspections, providing a sophisticated and holistic approach to infrastructure management. The ability to visualize, monitor, and analyse structures in real-time has revolutionized traditional workflows, offering a proactive and data-driven solution to maintenance and safety challenges. As the technology advances, its widespread adoption promises a future where infrastructure inspections are not only more efficient but also safer and more cost-effective, ensuring the longevity and reliability of our critical infrastructure assets.